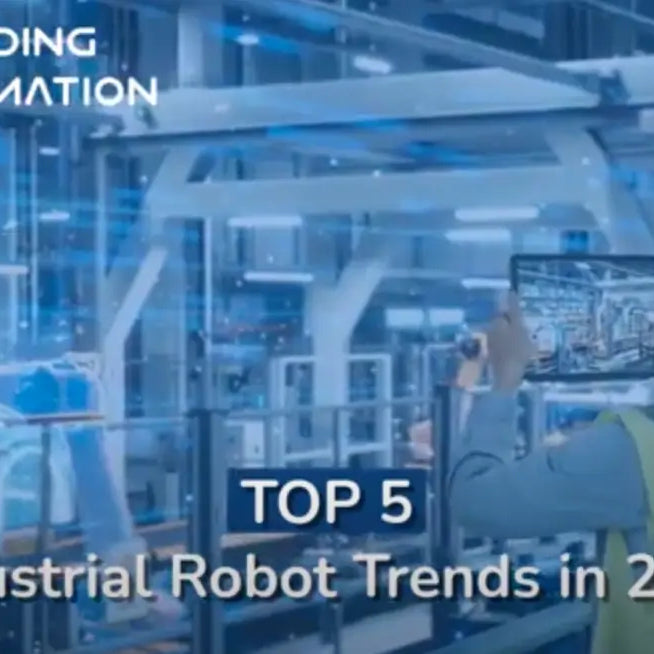
Orders & Worldwide
Orders & Worldwide
In the realm of modern manufacturing, industrial robots have become indispensable for their precision, efficiency, and ability to perform tasks in environments that may be hazardous to humans.
Understanding the structure and classification of industrial robots is crucial for engineers, manufacturers, and businesses looking to integrate or optimize robotic systems.
This article aims to demystify the world of industrial robots by delving into their composition, exploring different classification criteria, examining the industry chain, and discussing the working principles that drive these technological marvels.
Industrial robots primarily consist of three fundamental components: the main body, the drive system, and the control system.
The main body, which includes the base and the actuating devices, consists of the arm, wrist, and hand, with some robots also featuring a walking mechanism. Most industrial robots have 3 to 6 degrees of freedom, with the wrist typically having 1 to 3 degrees of freedom.
The drive system encompasses the power source and transmission mechanism, with the core components being the reducer and servomotors, which are used to generate the appropriate movements in the actuating devices.
The control system issues command signals to the drive and actuating systems according to the input program and performs control functions.
There is no internationally designated standard for the classification of industrial robots, but they can be categorized based on payload weight, control method, degrees of freedom, structure, and application field.
The industrial robot industry chain mainly comprises robot component manufacturers, robot main body manufacturers, agents, system integrators, and end-users. The main body is the core of the robot industry chain.
Typically, main body companies design the robots and write the software, then purchase through agents and sell to system integrators, who in turn face the end customers. Some main body companies and agents also act as system integrators.
Geographically, Europe and Japan firmly hold the industrial robot market, with Japan and Germany leading the world in industrial robot technology, mainly due to their first-mover advantages and technological accumulation.
Japan has strong technical barriers in the research and development of key components of industrial robots, such as reducers and servomotors. German industrial robots have certain advantages in terms of materials, main body components, and system integration.
In terms of enterprises, ABB, FANUC, KUKA, and YASKAWA are the four major families of industrial robots and are the world's main suppliers of industrial robots, accounting for about 50% of the global market share.
The working principles of robots are quite complex. In simple terms, the principle of a robot is to imitate various human body movements, ways of thinking, and decision-making abilities. From a control perspective, robots can achieve this goal through the following four methods.
"Teaching and Playback" method: It teaches the mechanical arm how to move through a "teaching box" or by manually "guiding" it. The controller memorizes the teaching process, and then the robot repeatedly performs the taught movements over and over again, such as in spray painting robots.
"Programmable Control" method: Staff prepare control programs in advance according to the robot's work tasks and motion trajectories, then input the control program into the robot's controller. Once the control program is activated, the robot completes the tasks step by step as stipulated by the program. If there is a task change, it is very flexible and convenient to simply modify or rewrite the control program. Most industrial robots work according to the first two methods.
"Remote Control" method: A person controls the robot with a wired or wireless remote control to complete a task in places that are difficult or dangerous for humans to reach. Examples include riot control robots, military robots, and robots working in environments with nuclear radiation and chemical contamination.
"Autonomous Control" method: This is the most advanced and complex mode of robot control. It requires the robot to have the ability to recognize the environment and make autonomous decisions in complex, unstructured environments, essentially possessing some intelligent behaviors akin to humans.
Taking a six-axis vertical articulated robot as an example (as shown in the figure below), through the robot controller and its control system, it is possible to achieve rotational motion of the S-axis, tilting of the lower arm on the L-axis, tilting of the upper arm on the U-axis, horizontal swinging of the arm on the R-axis, pitching of the wrist on the B-axis, and rotational motion of the wrist on the T-axis, realizing the operation and coordination of the six axes.
When a centralized control system is used, the control principle will be as shown below:
And if a distributed control system is used, the control principle will be as shown in the figure below:
As the industrial manufacturing sector continues to upgrade and new technologies emerge, robot manufacturers must also consider the usage needs of their end-users during the production process. For instance, when it comes to the upgrade and transformation of some factories and production lines, robot manufacturers also need to adapt to market changes and make corresponding adjustments.
Industrial robots represent the forefront of automation technology, offering a myriad of benefits that include increased productivity, improved quality, and enhanced safety. By dissecting the anatomy of these robots, we've uncovered the intricate systems that allow for their versatile applications.
The classification of industrial robots provides a framework for understanding the diverse range of capabilities and specializations within the field. Moreover, the industry chain highlights the collaborative ecosystem from component manufacturing to end-user implementation, emphasizing the importance of each link in the chain.
As we look to the future, the evolution of industrial robots will undoubtedly continue, propelled by advancements in artificial intelligence, machine learning, and materials science.
Manufacturers face the challenge of not only keeping pace with technological innovations but also adapting to the ever-changing market demands and regulatory landscapes. It is through continuous improvement, strategic adaptation, and a commitment to excellence that the industry will maintain its trajectory of growth and innovation.
Leave a comment on this topi